As one of the high speed decanter centrifuge manufacturer in China, GN solids control can produce different types, different size and different treating capacity centrifuges machine, by centrifuge sizes, we have 9 inch bowl centrifuge, 14 inch bowl centrifuge, 18 inch bowl centrifuge, 22 inch bowl centrifuge, 30 inch bowl centrifuge, the centrifuge bowl length diameter ratio available is 2, 3 or 4 series, so each centrifuge bowl with different bowl length for widely used. By centrifuge applications, we have centrifuge for T series dewatering type, Y series separation type and C series clarifying type centrifuges. The applications of GN centrifuges, including drilling fluids cleaning, drilling waste treatment, oil sludge treatment, industrial waste slurry treatment, construction mud cleaning, etc. By driving methods, we have VFD control decanter centrifuge and full hydraulic drive decanter centrifuge. Besides, we also produced 2 phase separation, 3 phase separation centrifuge; and horizontal centrifuge, vertical centrifuge ( 3 phase or 2 phase disc separator). For your different treating capacity and treatment requirement, we will offer different model centrifuge.
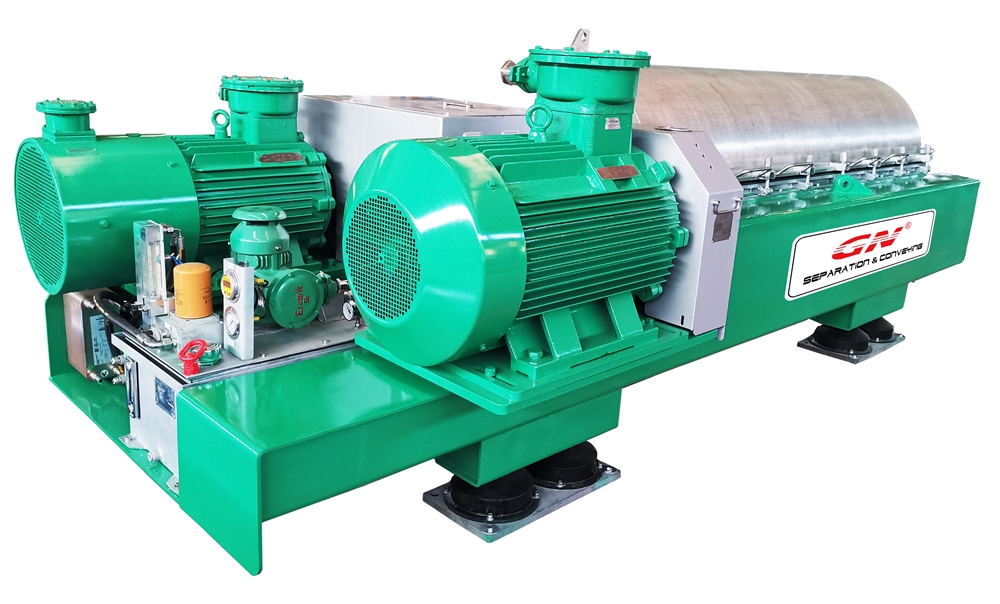
As a manufacturer of high speed decanter centrifuge, we have specific standard for its performance requirement in manufacturing as per industry standard.
- The centrifuge shall be free of collision and abnormal sound when it is started to the rated speed
- The starting time and maximum starting current when the centrifuge starts to the rated speed shall meet the design requirements.
- The bowl speed shall not be less than 97% of the rated speed
- Under unloading condition, the vibration speed of low speed centrifuge shall not be higher than 4.5mm/s, and that of high speed centrifuge shall not be higher than 7.1mm/s
- Under unloading condition, the temperature of main bearing shall not exceed 70 ℃, and the temperature rise shall not exceed 35 ℃.