We can use both 3 phase decanter centrifuge package and 3 phase disc separator package for oil sludge treatment, the pre-treatment equipment for both of them are shale shaker for primary screening of coarse solids. We will select proper 3 phase separation package according to client’s requirement and oil sludge conditions.
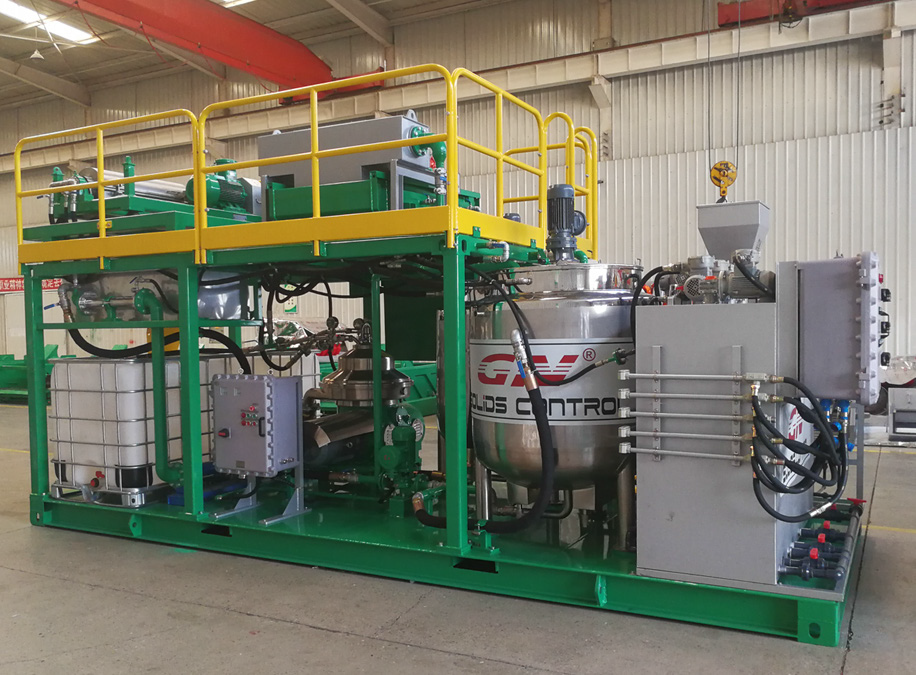
The comparison of 3 phase disc separator and 3 phase decanter centrifuge is as below:
The max G force of 3 phase disc separator is up to 12000G, but for 3 phase decanter centrifuge is up to 3000G.
The 3 phase disc separator will be used after 2 phase decanter centrifuge or 3 phase decanter centrifuge. The treatment result for oil on solids , water in oil, oil in water is in high level.
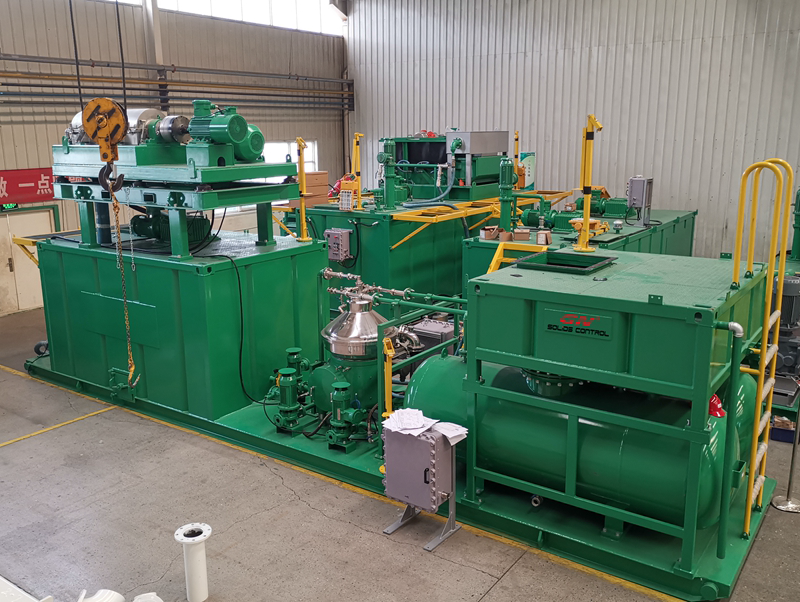
The 3 phase decanter centrifuge can be used separately after primary screening of coarse solids, if the budget is limited, and the treatment result of oil on solids, water in oil, oil in water is not high.
The operation of 3 phase disc separator is complicated and need cleaning frequently, but operation of 3 phase decanter centrifuge is more simple with automatic cleaning. So if the user need to get high quality oil and water, and no limit for the investment, 3 phase disc separator package is proper option. If the investment is low and less quality oil water is required, we will select 3 phase decanter centrifuge package.
Except for 3 phase disc separator package and 3 phase decanter centrifuge package, GN also provide accessories for them, including vacuum pump package to pick up the oil sludge, pre-mixing tank for pre-treatment including chemical jetting, heating and mixing, coarse screening module, chemical dosing unit and oil water storage tank, etc.
If you need a customized oil sludge treatment solution, pls contact with GN solids control.