The solids vacuum pump is mainly used for drilling cuttings transfer, mud tank cleaning, drilling rig platform cleaning, waste pit cleaning, etc. applications by oil service company and drilling companies.
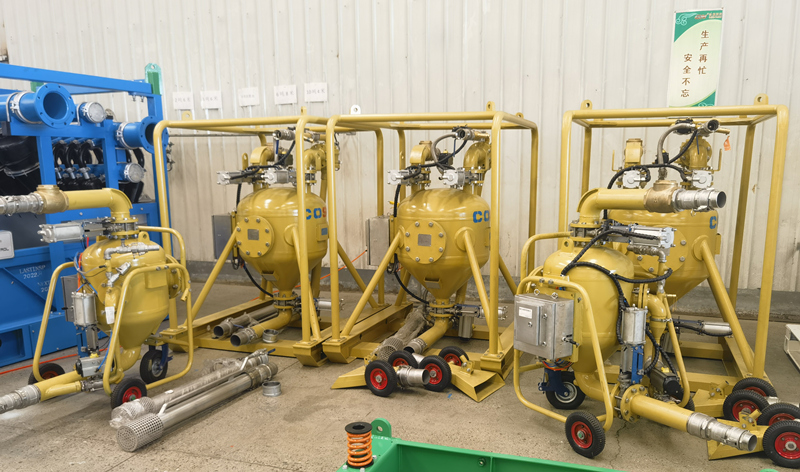
GN solids control have different model vacuum pumps for option based on their requirement. GNSP-40B max capacity is 40m3/h, GNSP-20B max capacity is 20m3/h, GNSP-10B max capacity is 10m3/h. The design capacity of the vacuum pump is nominal capacity, it will varied based on different material, suction and discharge distance and depth. The air supply should be sufficient for vacuum pump reliable operation. The drilling waste can be picked up automatically and transferred to drilling waste management system. Another method to transfer drilling cuttings is screw conveyor, due to place limit and rig site layout, the screw conveyor system may not be used, then solids vacuum pump can be used instead.
The suction process is that the air compressor provide the air into the vacuum generator, which produces negative pressure in the pump body and suck the drilling waste from the suction pipe. The discharge valve is in close condition. According to suction time, the pump will suck material automatically.
The discharge process is that close the valve of vacuum generator, the air flow to the pump body to produce positive pressure inside the pump body. The discharge valve is open, and the drilling waste is pushed out by positive pressure to the expected area.
The features of GN vacuum pump:
- It can be used for hazardous area application, since it is 100% air operation pump. But air compressor is required for air supply.
- The suction horizontal distance is up to 50m, the discharge horizontal distance is up to 500 ~ 1000m.
- The solids size allowed to enter into vacuum pump is up to 50mm or 75mm, the solids content is up to 80%.